(I am still in sprint novel-writing mode this week. More news on that later. In the mean time, a few news chunks from the world of the electricar.)
Both of these stories beg the question: will the electric car be running out of Detroit or will it be put together by hobby guys, like computers used to be. My money is on Detroit (or the other mass market industrial centers) but this does give one cause for pause. In either case, the future is looking brighter and brighter for the electric car. Or at least a lot brighter than it is for the End of The World, which seems to have failed to happen.
At present, in order to meet sudden surges in demand, power companies have to bring additional generators online at a moment's notice, a procedure that is both expensive and inefficient. If there were enough electric vehicles around, though, a fair number would be bound to be plugged in and recharging at any given time. Why not rig this idle fleet so that, when demand for electricity spikes, they stop drawing current from the grid and instead start pumping it back?
The idea, known as vehicle-to-grid (V2G), sounds great in theory. But what about in practice? To find out, Willett Kempton and Nathaniel Pearre, of the University of Delaware, has for the past three years been running a fleet of seven electric cars linked up to his local electricity company's servers by a wireless system that monitors their activity, in order to predict when each car is likely to be available as a power supply.
What the power company would be paying for is not so much the electricity itself as the availability of that electricity at zero notice. At the moment, peaks in demand have to be sated by firing up expensive rapid-response generators, such as gas turbines. Speed of availability is as important as total capacity. Battery-driven cars, if plugged in appropriately, provide power instantly—faster, even, than a stand-by power station. That is where they truly score. And, for that reason, owners would actually be paid a tariff related to when and for how long their cars were available for the power company to tap. In Delaware, this amounts to about 30 cents an hour. Add in a fixed fee payable just for being part of the system and Dr Kempton and Dr Pearre think an income of $4,000 a year per car might be possible. That is a sum far greater than the $225 that Nissan, for instance, thinks will be the average annual cost of the electricity needed to power one of its Leafs.
(Economist 17 may)
IN THE early days of the automobile there were several hundred manufacturers in America and many more in other parts of the world. But now carmaking is dominated by just a dozen or so global firms. Yet technological change can disrupt established industries by lowering the barriers to entry and letting in newcomers. There are signs of that happening in carmaking.
Using the latest electric-vehicle technologies and new manufacturing techniques, Tesla sprang from Silicon Valley with an electric sports car. Fisker, another new Californian firm, is building a hybrid luxury car called the Karma. Other firms have projects under way ranging from electric commuter cars to conversions of existing vehicles. And yesterday a tiny company called Delta Motorsport unveiled not just one but five working prototypes of its 150mph (241kph) E-4 Coupe, developed and built with a minuscule £750,000 ($1.2m) budget.
“Some of the big carmakers are interested,” says Simon Dowson, the firm’s managing director. “They wonder how we did it.” Delta Motorsport was formed in 2005 by Mr Dowson and his technical director, Nick Carpenter. They have just ten employees. But they are based at the Silverstone motor-racing circuit in Britain, which provides a clue as to how they pulled it off.
The company wanted to apply the same lean and rapid development techniques used by the motor-racing industry to produce an electric sports car. They did the design, engineering and assembly work but subcontracted the manufacturing of parts to other suppliers in what Mr Dowson describes as “Motorsport Valley”, an area stretching through the middle of England. This is where many vehicle-engineering firms and most Formula One racing teams are based.
The Delta E-4 Coupe, like all preproduction prototypes, still needs work. But the cars are nippy, handle well and have a striking design, with “butterfly” doors that swing up and open. The prototypes, fitted with a smaller battery than the 48 kWh lithium-ion battery pack planned for the fastest version, are not yet capable of delivering what Delta expects to be 0-60mph in under 5 seconds and a range of 200 miles on a single charge. Nevertheless, the car does have four seats, can be fully recharged in eight hours from a conventional 13 amp mains socket and would meet European crashworthiness tests.
The prototypes use powerful direct-drive electric motors developed by Oxford YASA Motors, another Motorsport Valley firm. At present two electric motors are used, one powering each of the rear wheels. But motors could be fitted to the front wheels as well to provide four-wheel drive.
The monocoque (the basic body and chassis) is built using tough but light composite technology. Some parts are built using carbon fibre, other bits from glass fibre. As such, the monocoque weighs only about one-third of what it would if built from steel. The composite materials can also be used in a factory-type production process, says Mr Dowson. Indeed a number of carmakers are looking at ways to mass-produce cars built from composites, including BMW, which is developing a range of urban electric vehicles. Because manufacturing with composites does not require huge investment in massive presses to stamp out parts in metal, BMW is also looking at the possibility of satellite production, so that body parts can be built economically in more than one location. Unlike Delta, though, BMW has yet to show off working prototypes.
The new manufacturing methods make low-volume production runs more viable. Jaguar announced this week it would put into production its C-X75 hybrid, a 200mph supercar. It will build just 250 examples in a partnership with Williams F1, also a Motorsport Valley company. The C-X75 will have a carbon-fibre chassis and cost more than £700,000. The original concept used two micro-turbines to generate power for its batteries. The production car, however, will use a small internal-combustion engine instead while Jaguar and Bladon Jets, a British firm developing the idea, continue to work on the technology. Tata, Jaguar's parent company, has taken a stake in Bladon Jets.
If a few hundred E-4s were built they might cost about £50,000 or more, says Mr Dowson, although larger production volumes would bring the cost down. The company designed the car to be built at a rate of 10,000 or more a year. But the firm does not have the resources to put the E-4 into production and is looking for other groups or investors interested in helping it take the idea forward. A few years back, the car industry used to reckon it cost $1 billion or more to put a new car into production—and at least 500,000 would need to roll off the production line every year to produce a return on that investment. Mr Dowson thinks they could start to put the E-4 into production for about £4.5m. That is the price of a handful of petrol-powered supercars.
(Economist 10 may)
HIL-GLE MIND ROT MODERN THRILLS QUALITY CREATIVE NEWSSTAND FICTION UNIT WONDERBLOG Shy people can contact us directly via email at Wunker2000 at Yahoo dot com.
Visit HIL-GLE Today!
Monday, May 23, 2011
Subscribe to:
Post Comments (Atom)
Search the Wonderblog!
Blog Archive
COMMIT TO INDOLENCE!
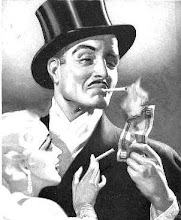
Ajax Telegraph, Chicago IL
No comments:
Post a Comment